Working with not-yet realized technology in a semi-trailer-sized package creates its own challenges that computer simulation cannot predict. In addition, expecting users to maintain this technology in enclosed spaces with adverse conditions yields poor usability and adoption. Over the course of six months, I rapidly prototyped the equipment using foam, cardboard, rope, wood, and in some cases the actual equipment. Engineering and the users were directed to go through usability challenges with the equipment. This included manufacturability, maintaining the equipment, climbing on the equipment, on-the-move drills, and documenting unforeseen scenarios. After I concluded the usability and manufacturability studies, our customer chuckled with joy to be included in the process. They also stated that this is the first time they were ever asked to give their expertise in developing such technology. Our company benefited from receiving multiple customer accolades for our innovative, user-centric approach.
I received several top awards for my innovative approaches, engineering collaboration, and forward-leaning concepts.

Above are a snapshot of the results from the tests conducted in the video. I was testing several, large cabling concepts with users. Each of the 2 cables weighed 200 lbs. and had to be lifted 5 feet in the air to where they were stored. This determined the direction engineering was taking for this trailer development.
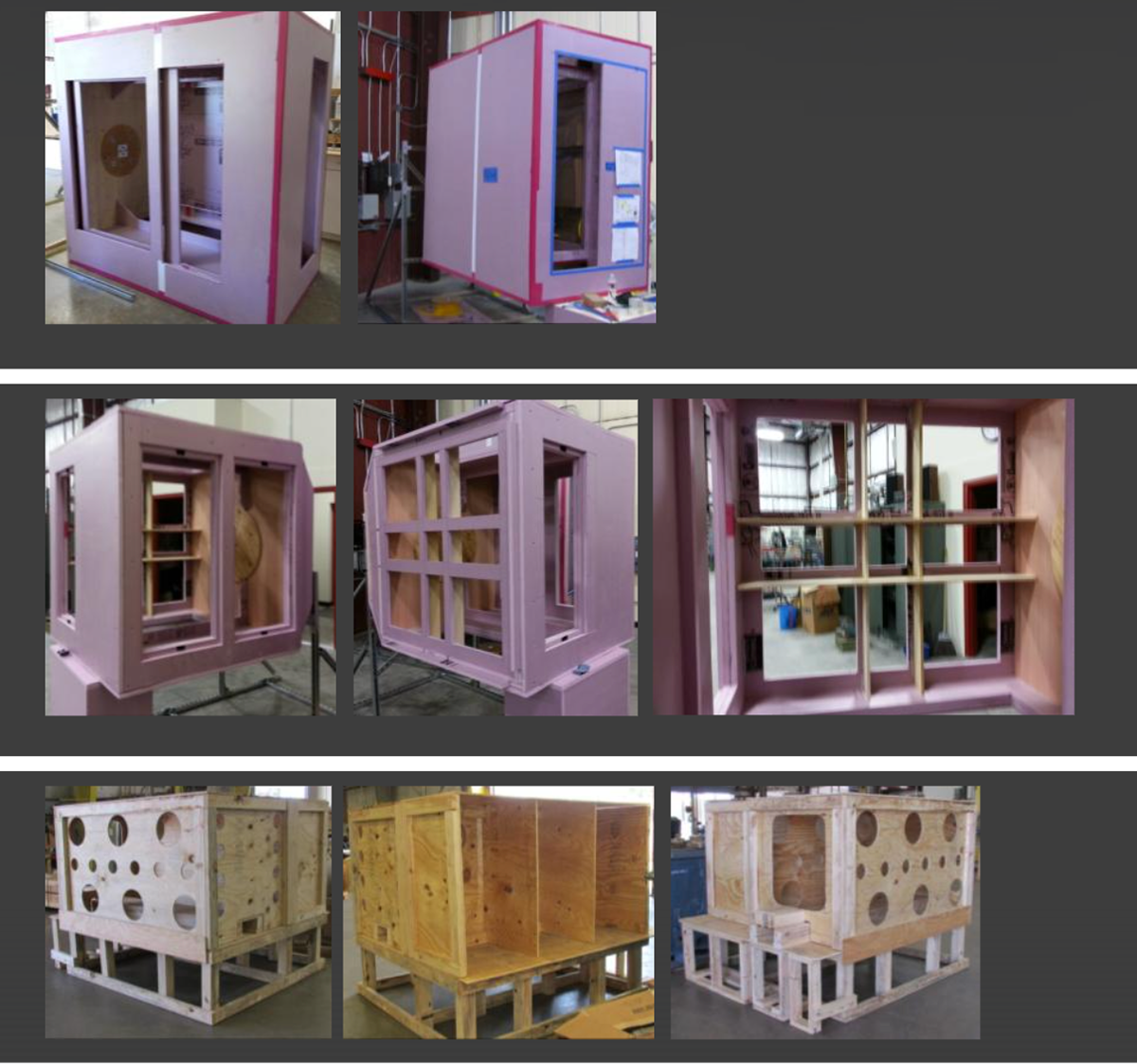
"head" and "base" units usability model
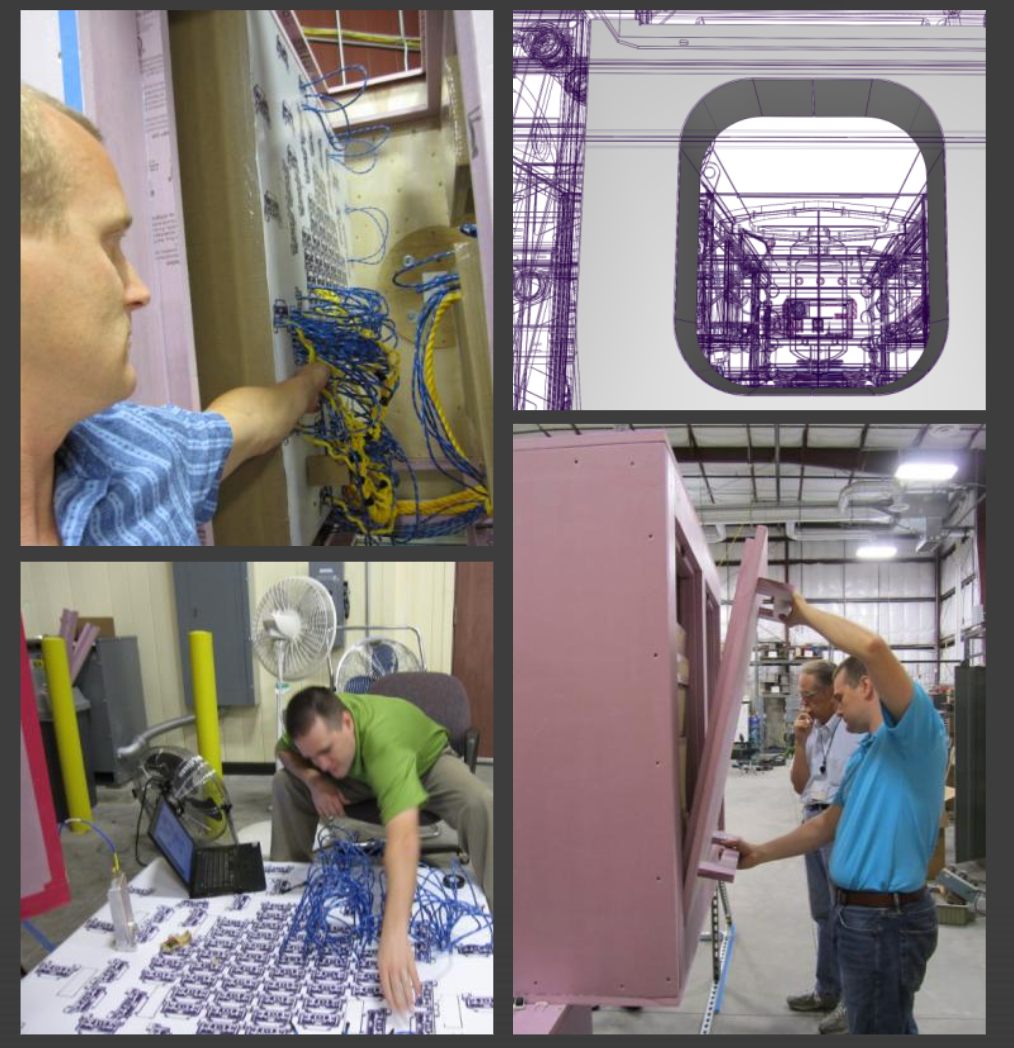
Capturing usability issues

Overview of the "head" usability model
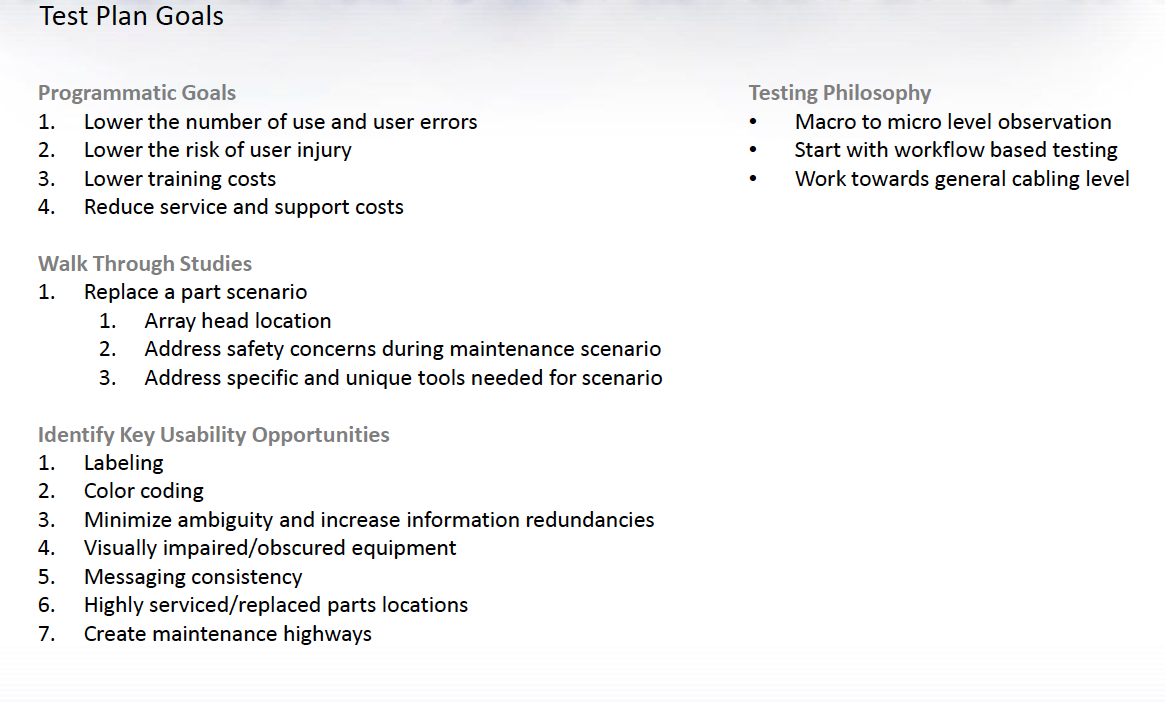
The test plan

Maintainability suggestions

Maintainer efforts
Maintainer control
Quick guide on back
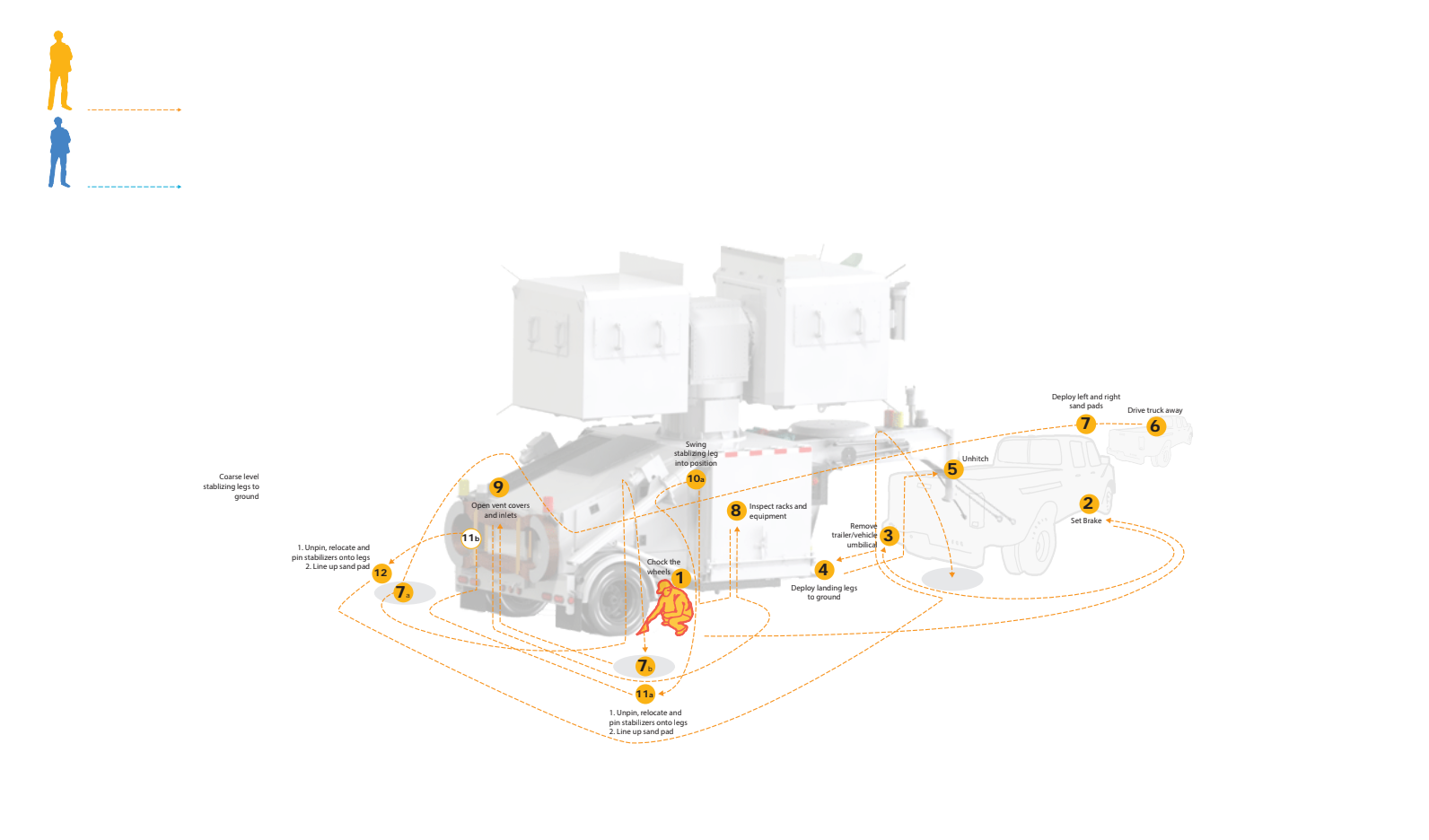
Set up diagram

Maintainer trade study
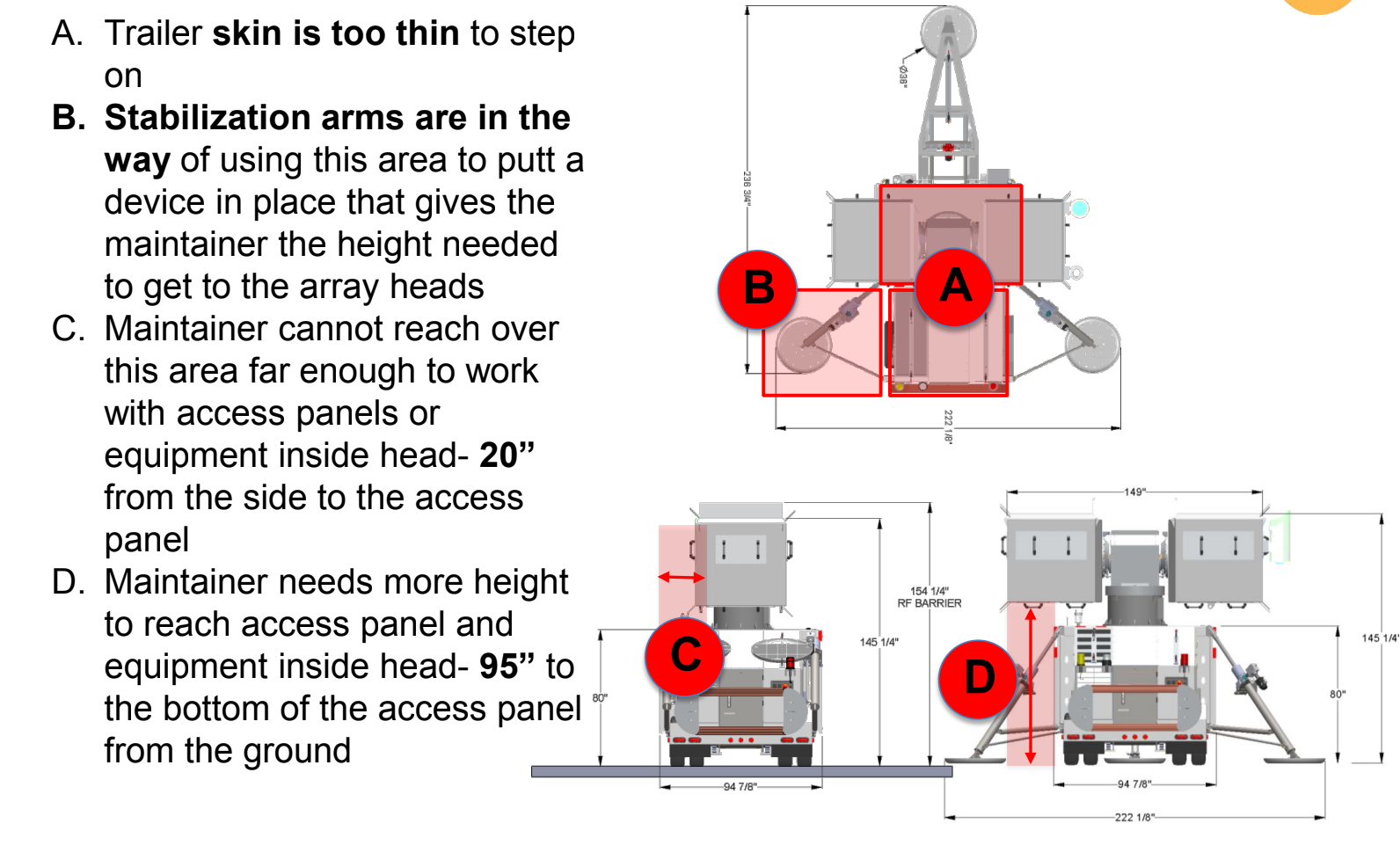
Maintainer best practices
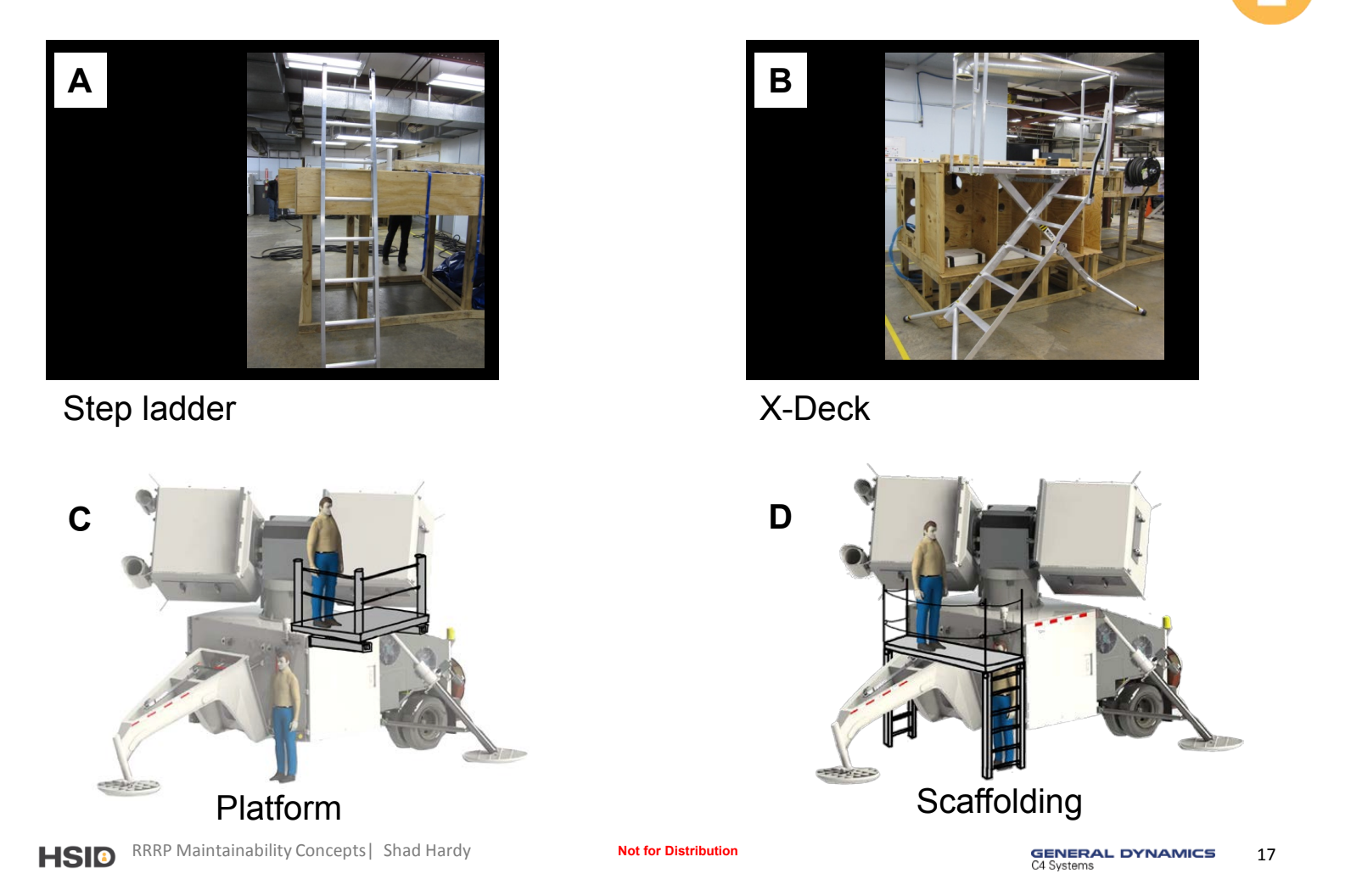
Ladder study
Various stages of user experience exercises and experiences all jammed into one section for your perusal.
corp website feature employee

Autonomous vehicle retrieval
Coast Guard mission evaluation
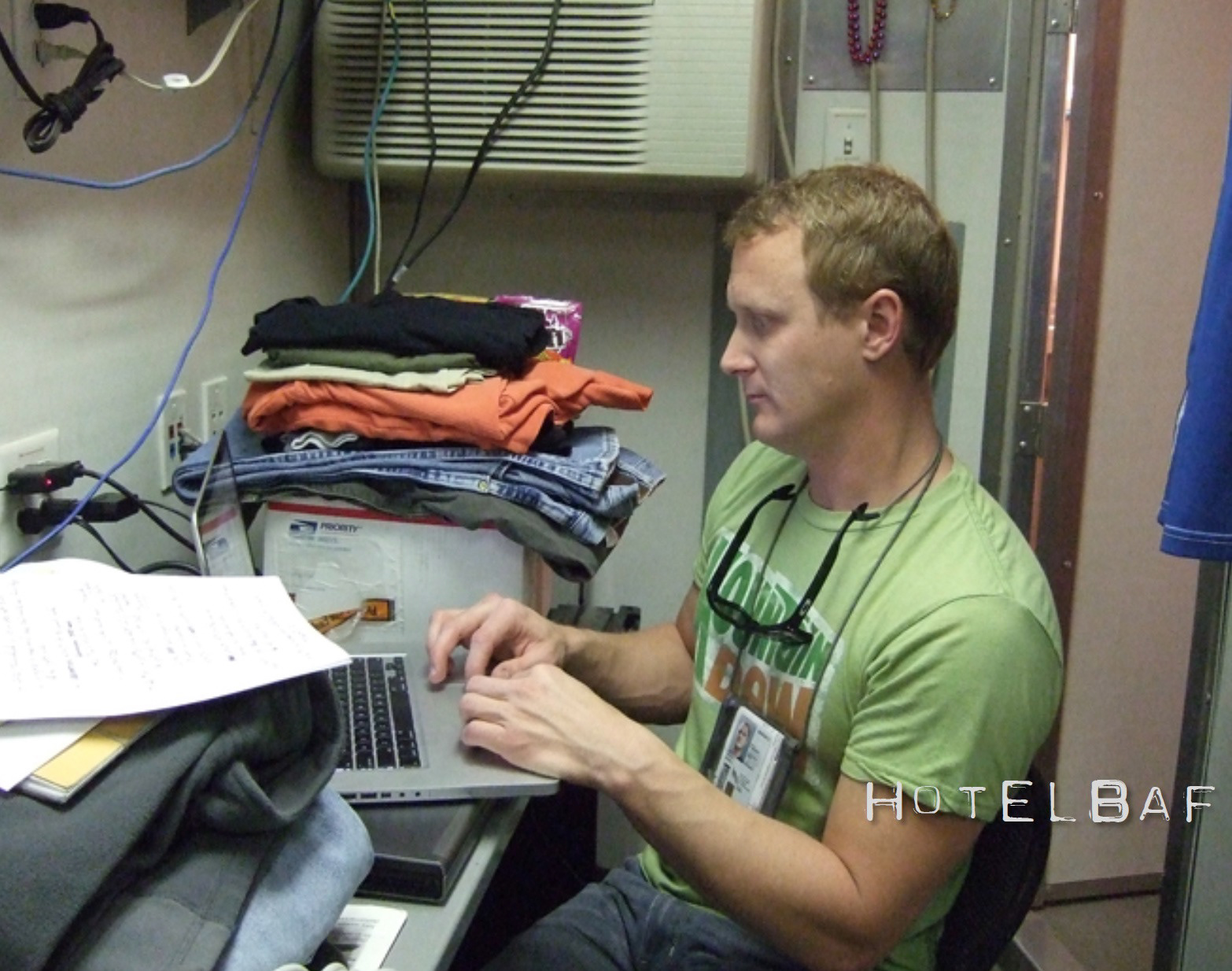
Afghanistan- Sending test docs home
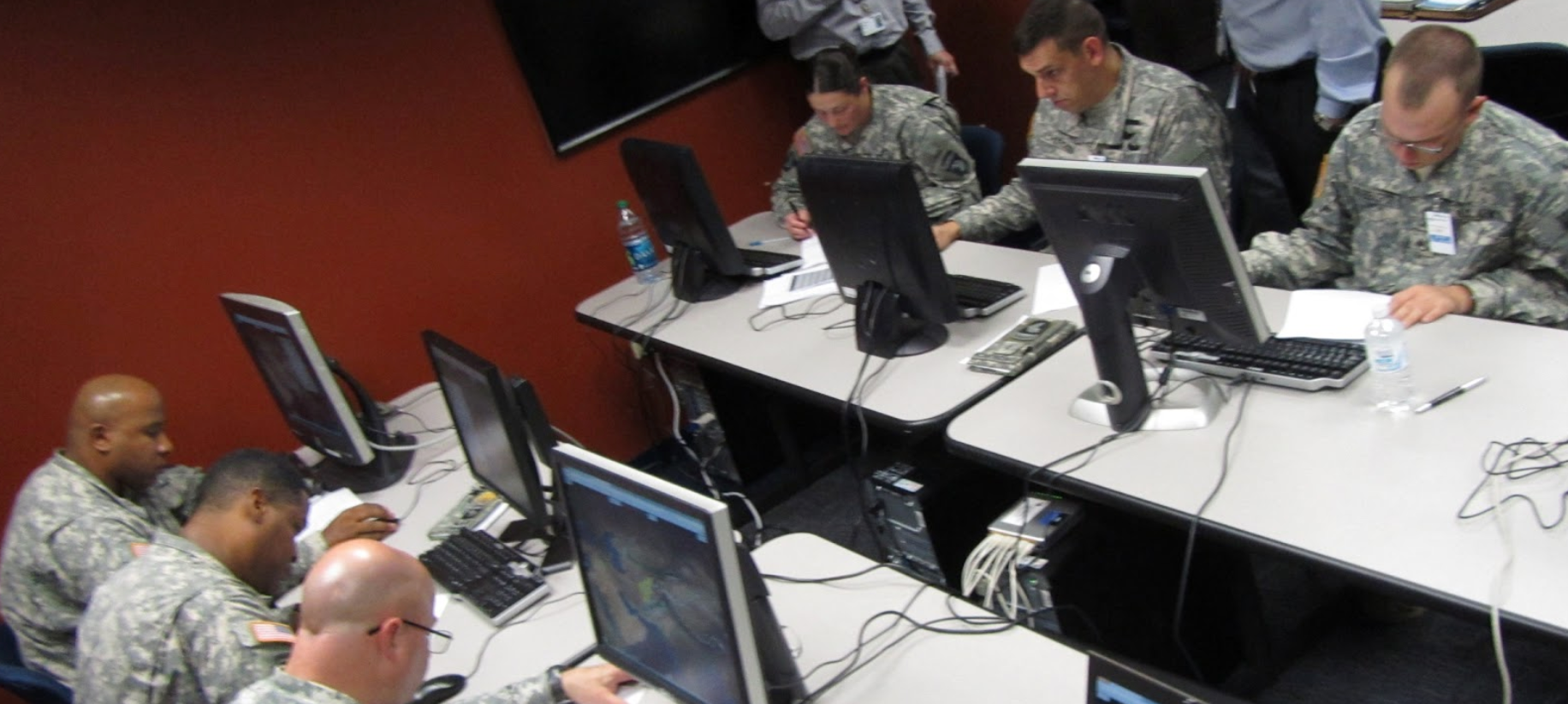
Large scale system usability testing (SUS, NASA TLX)
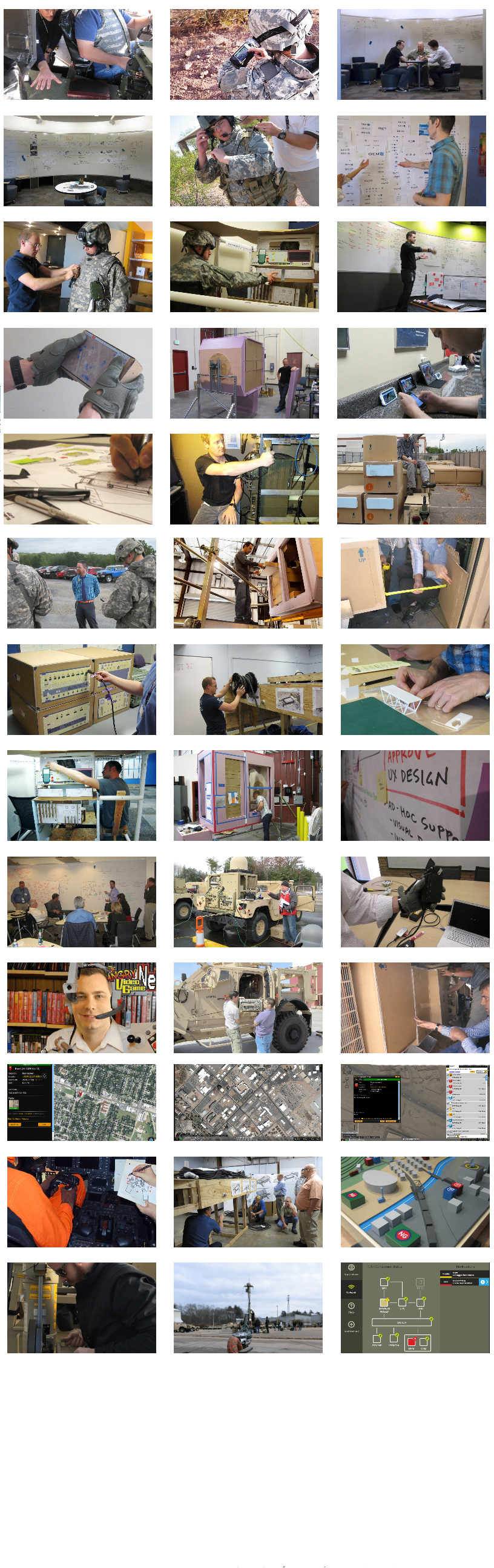
User participation

Human factors heuristic testing

Customer mission planning

System heuristics
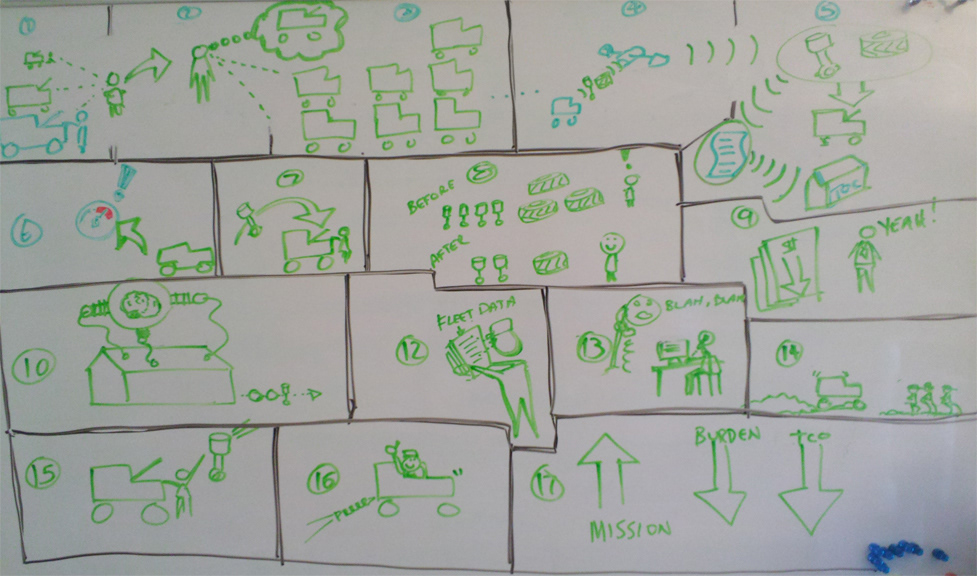
Mapping user journeys

Interface heuristics
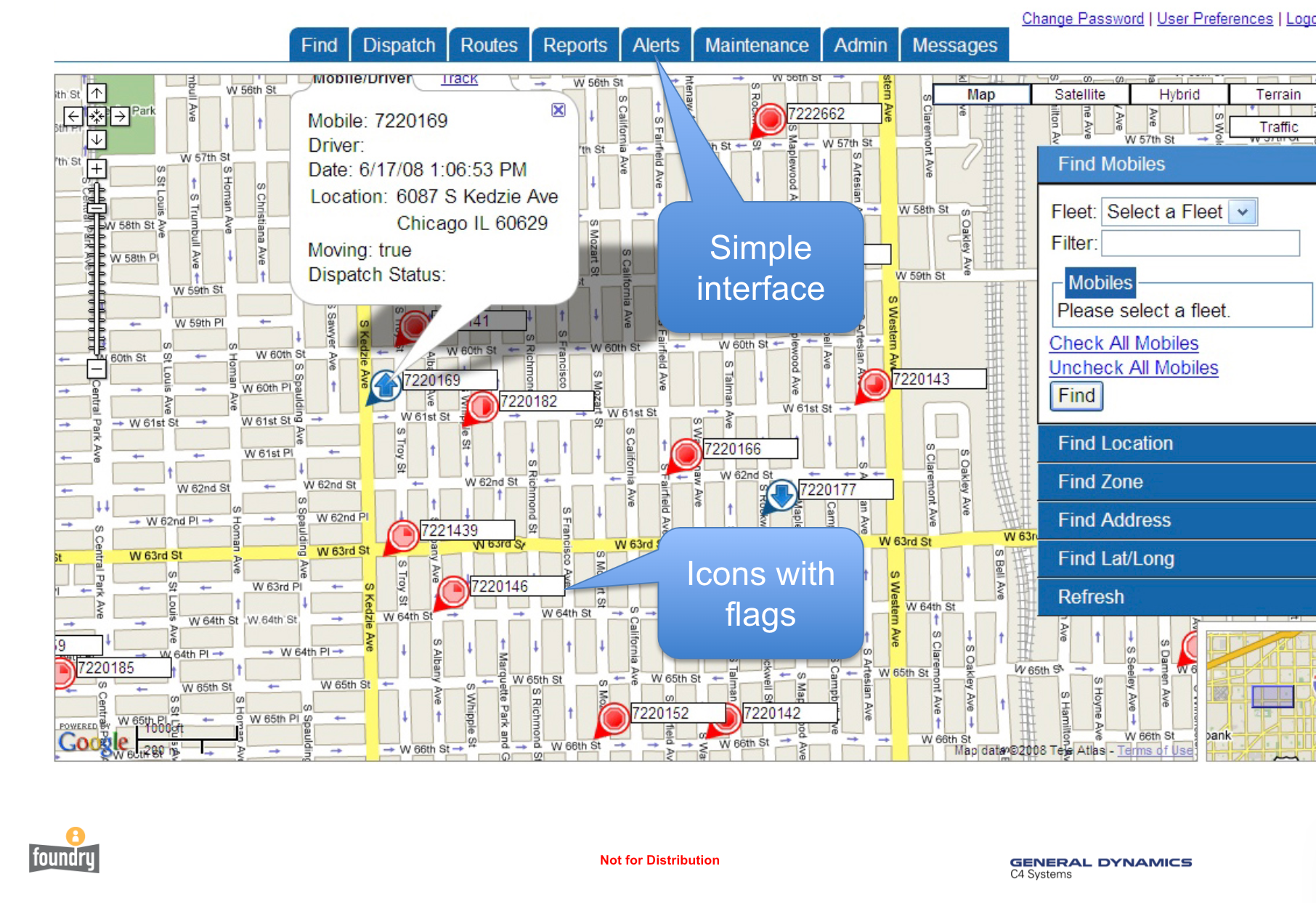
Interface heuristics

Engineering diagrams

Field testing UI
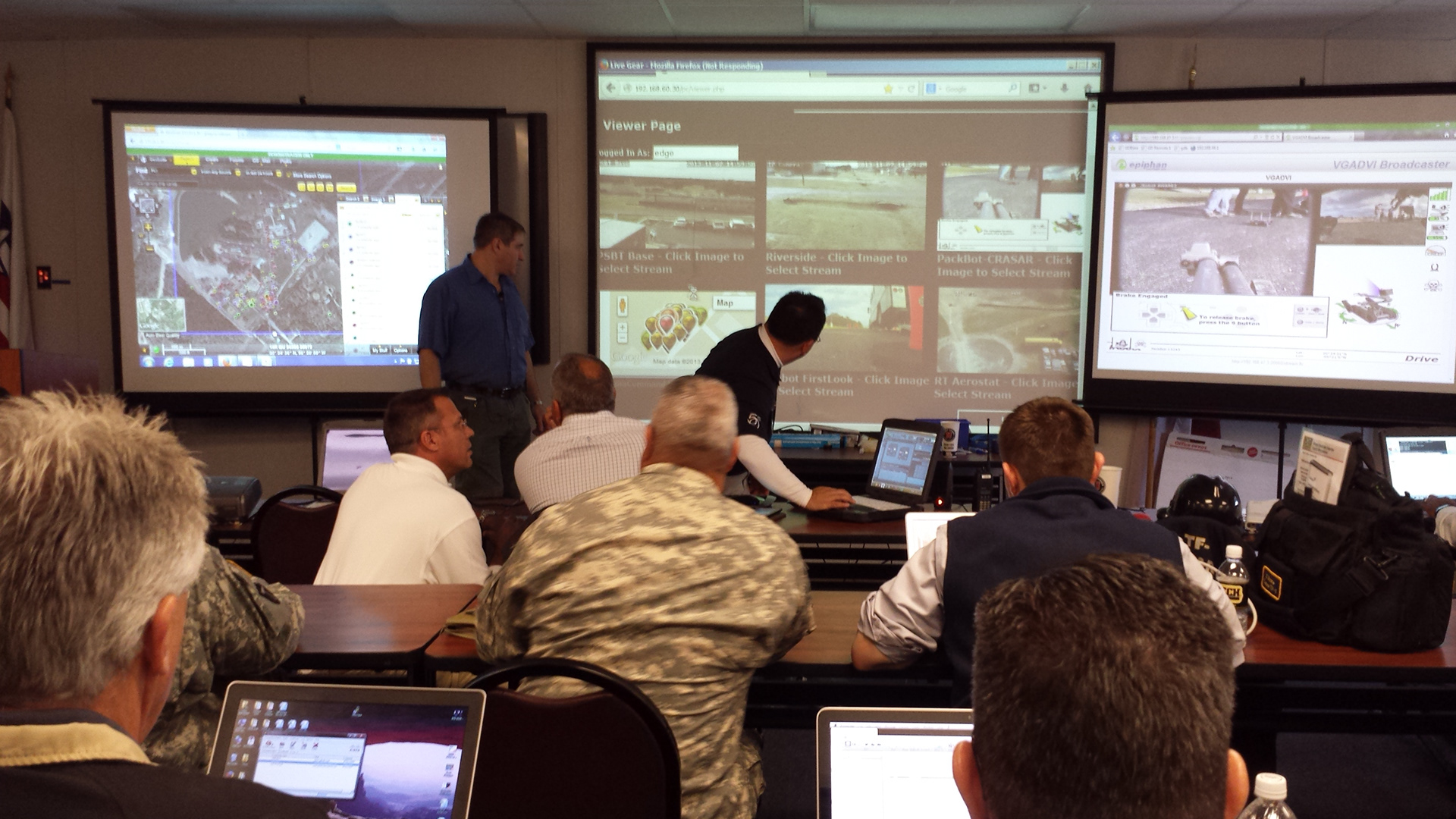
Command center heuristic
I was often tasked with understanding large-scale scenarios to tame their complexity. To do so, I interviewed multiple users from every part of a scenario. This helped the many multi-disciplinary teams and my team to focus on the functionality users most needed.


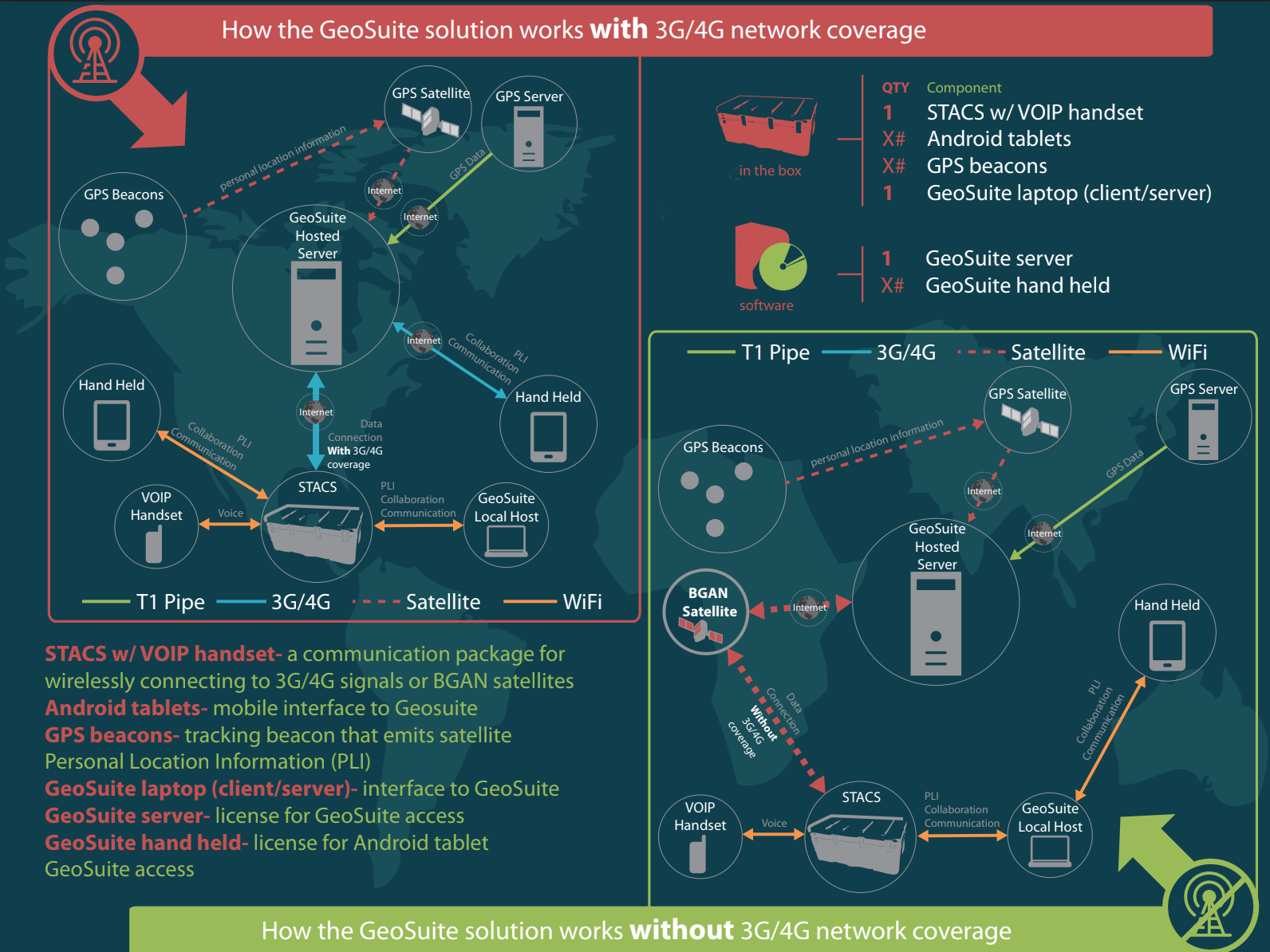
Aligning to the corporate process leads to long-term durable growth. At the time, the UX team was a unique part of the business. The slides below are part of the UX value proposition presented to senior leadership and customers in an effort to be in lockstep and enhance business efforts. The deck was extremely successful in first-time introductions. The response became overwhelming in bringing in new and additional work resulting in doubling our group's size.
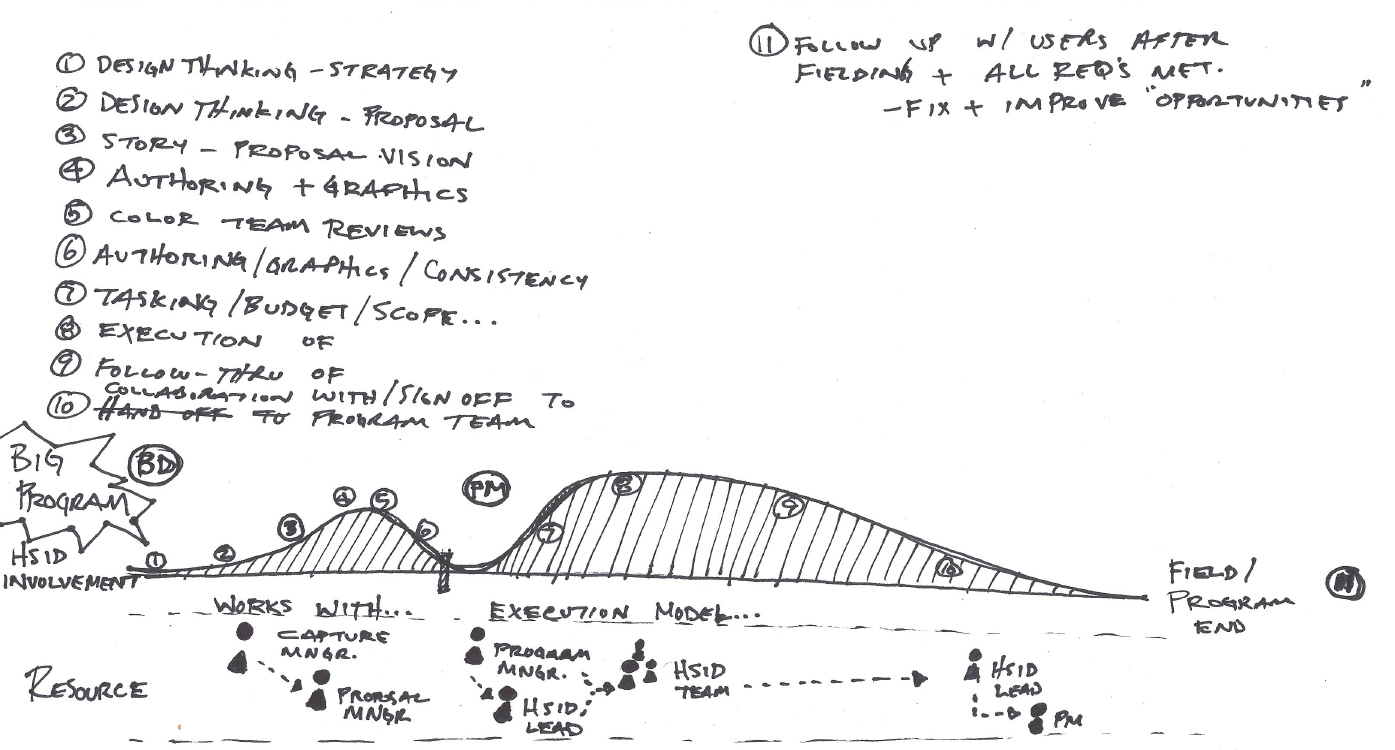
Deciding timing, work products and roles

UX process within Engineering process
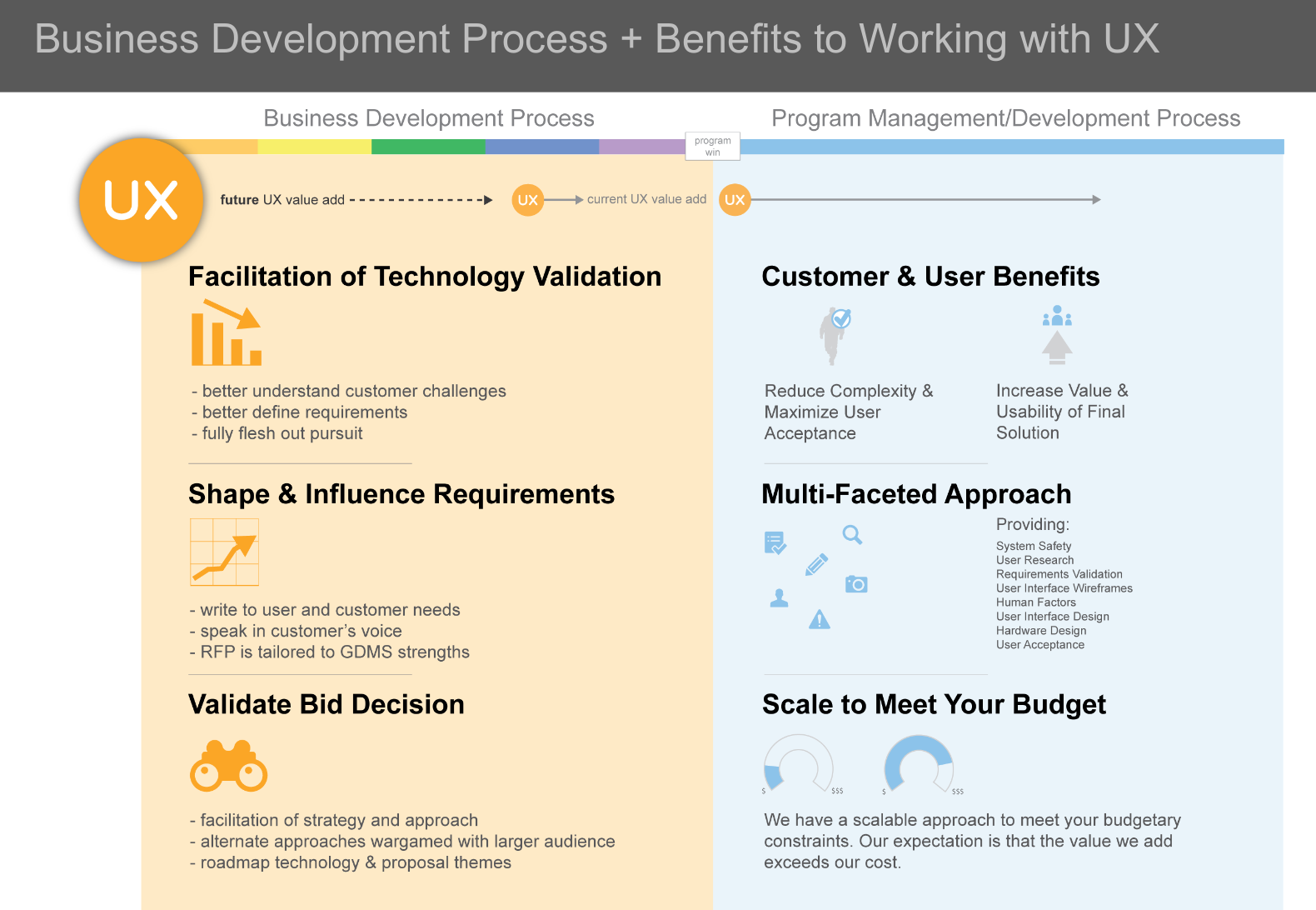
Value proposition to Engineering
Our Supply Chain team needed a new direction on their 5-year vision. They turned to a facilitated activity that I lead. After reading 4 supply chain books the night before, I was able to effectively move the needle during the day-long white boarding exercise. After identifying tools, processes, and resources, I was able to create a direction for the SCM. Several years later, the plan was still being used as the basis to drive change.

SCM alignment to the company
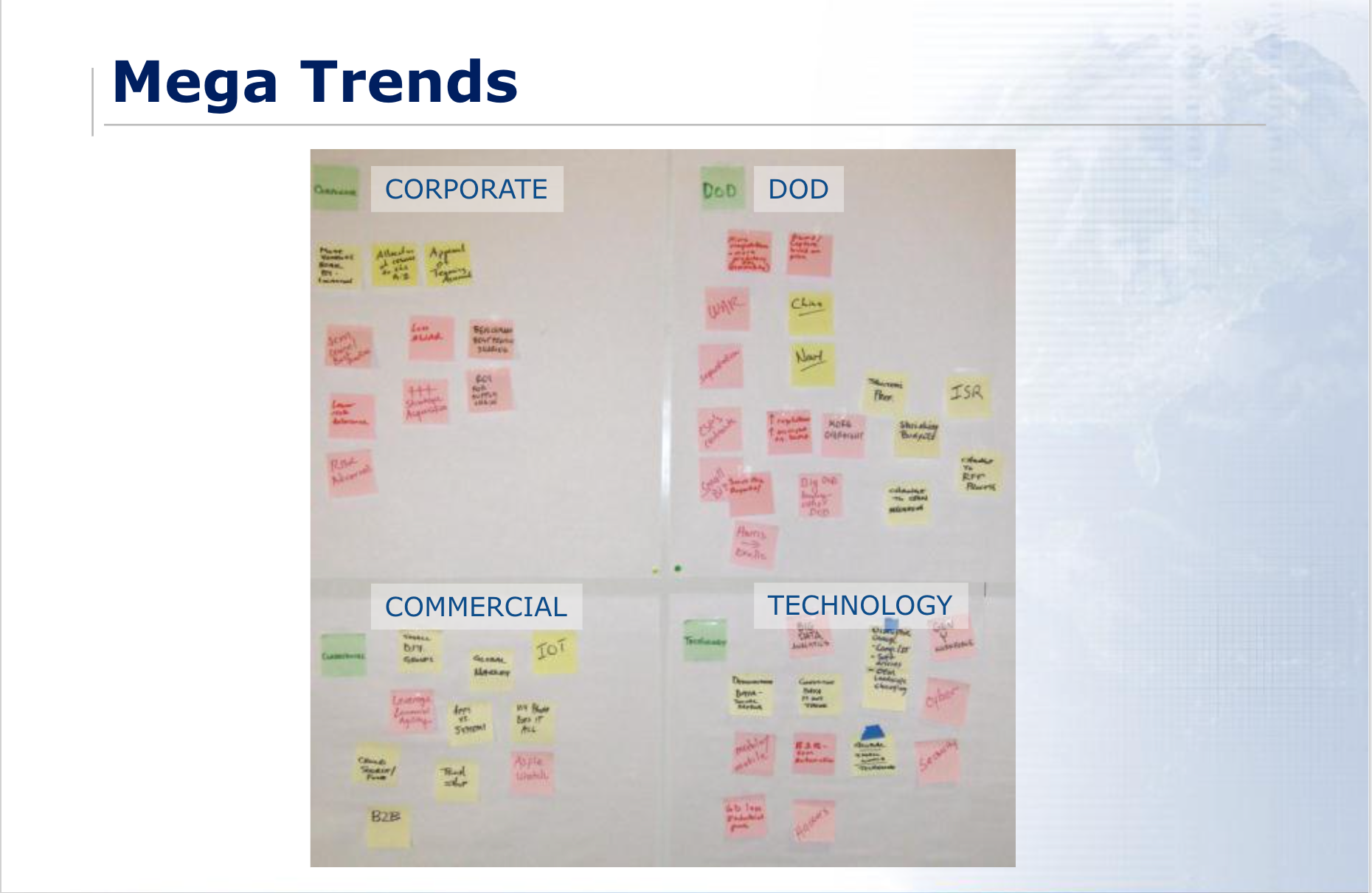
Supply chain trends
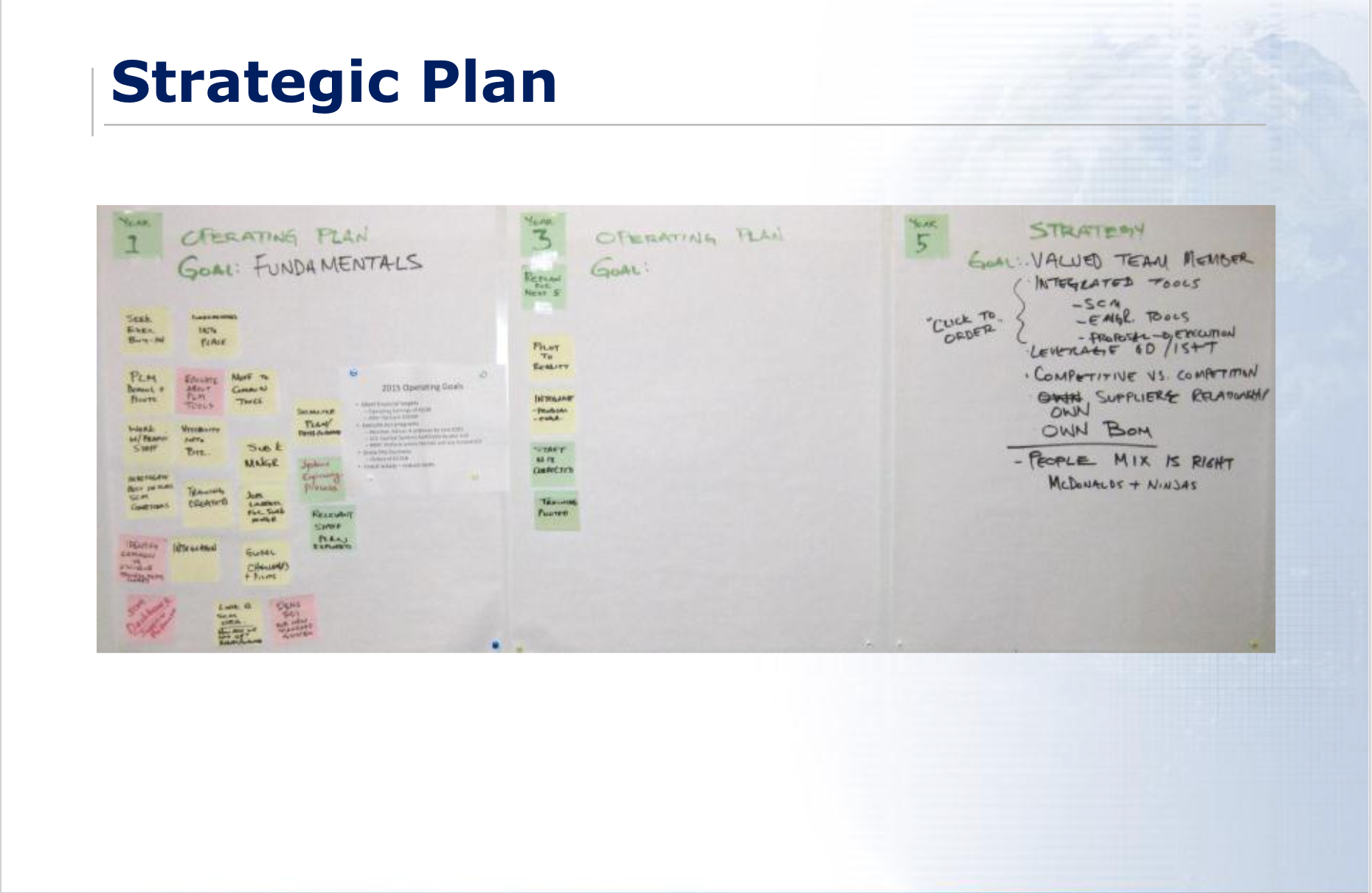
Identifying top priorities and planning
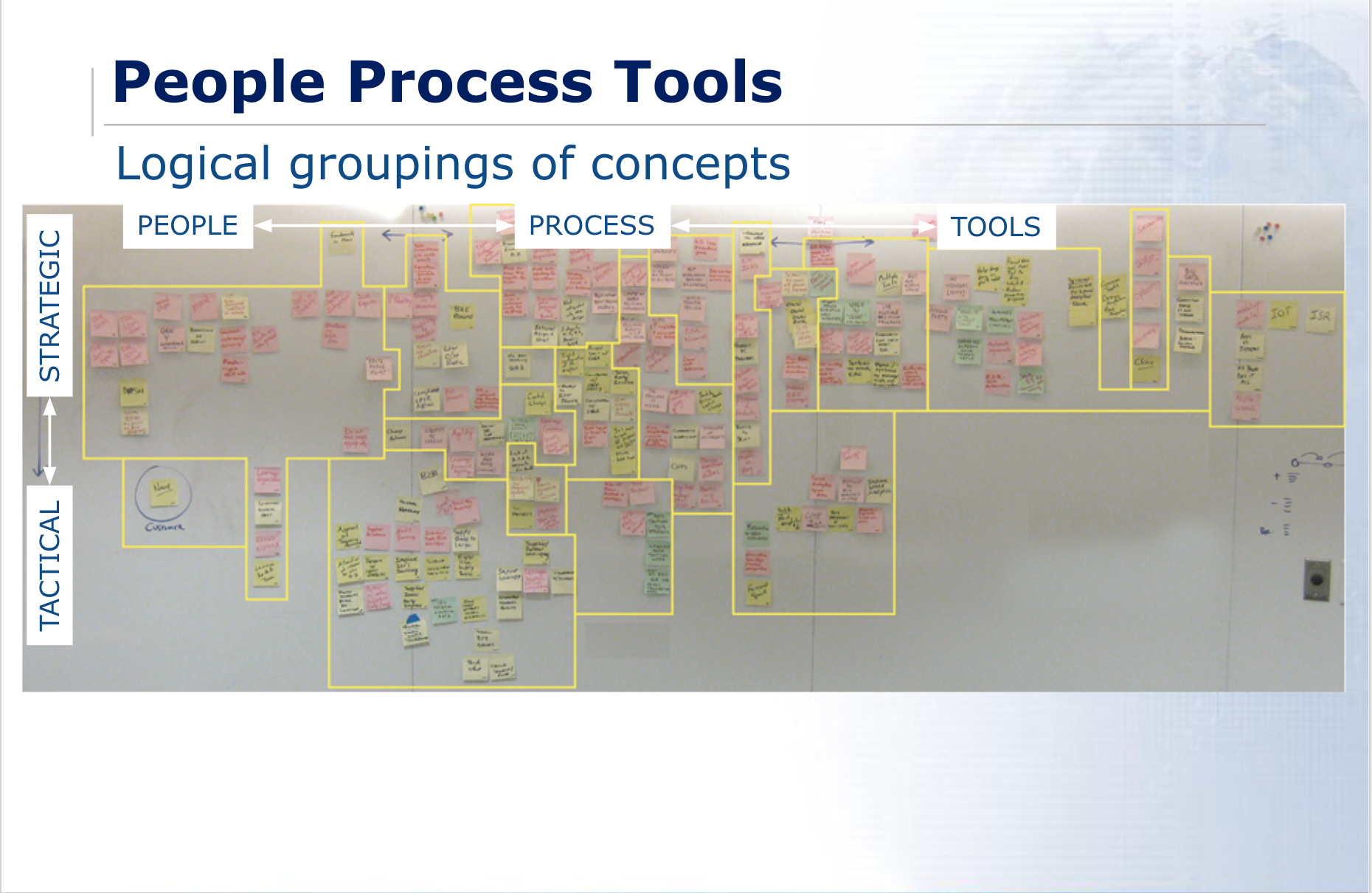
Identifying the supply chain attributes

SCM overview
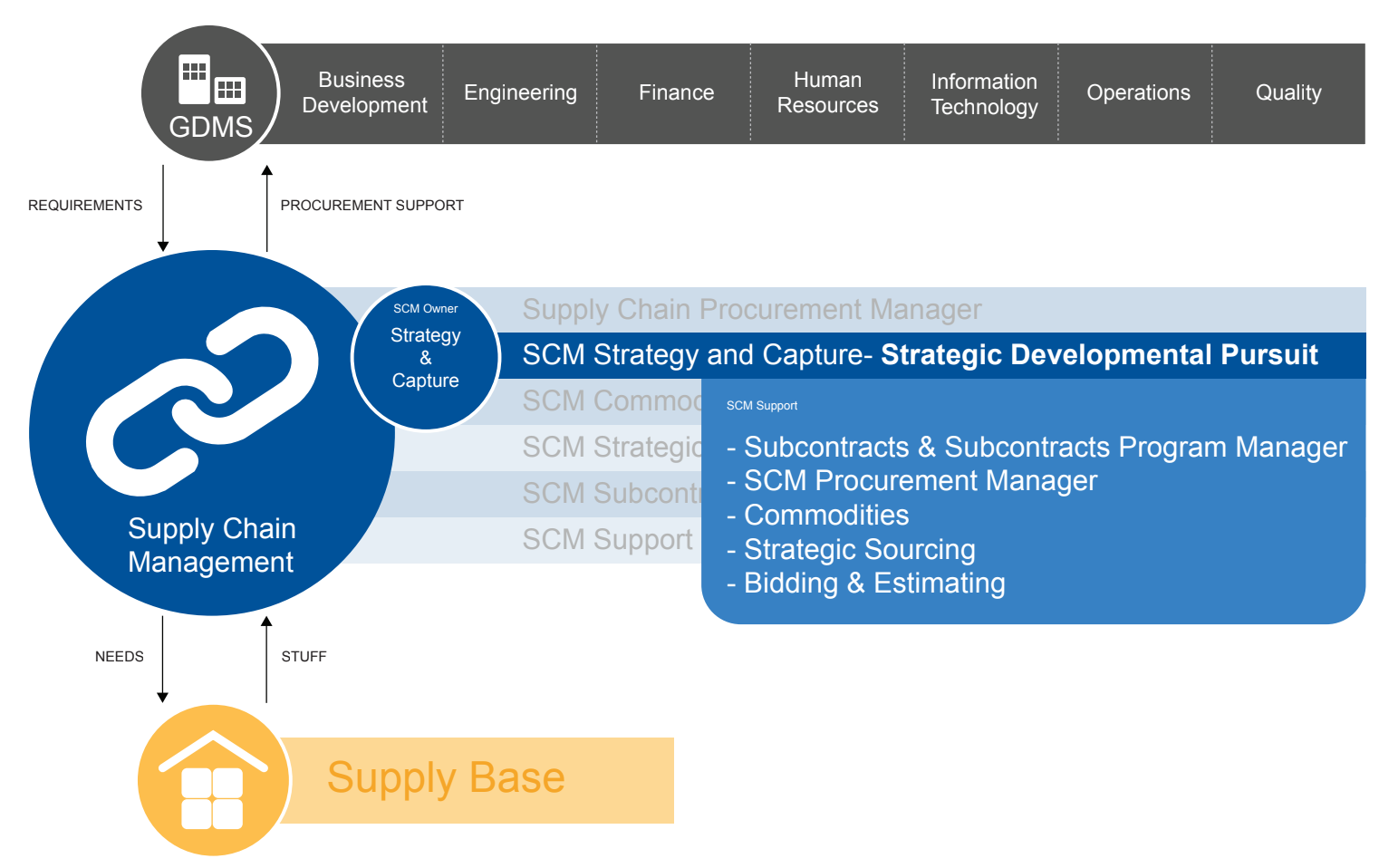